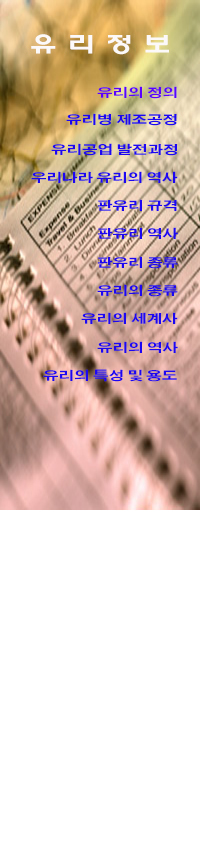
|
|

|
|
|

|

|
|
Å©¶ó¿îÛö(Crown Method)¿¡ ÀÇÇÑ Ã¢¹®À¯¸®ÀÇ Á¦Á¶´Â 3¼¼±â °æ, Áï °í´ë ·Î¸¶½Ã´ë¿¡ ½Ã¸®¾ÆÀο¡ ÀÇÇØ¼ °³¹ßµÇ¾ú½À´Ï´Ù. ÀÌ Á¦Á¶¹ýÀº
18¼¼±â ¸»±îÁö ¹øÃ¢ÇßÀ¸¸ç, ¿µ±¹¿¡¼´Â 20¼¼±â±îÁöµµ ÀÌ ¹æ¹ýÀ» ÀÌ¿ë, À¯¸®¸¦ Á¦Á¶ÇÏ´Â °øÀåÀÌ ÀÖ¾ú½À´Ï´Ù.
ºí·Î¿ì ÆÄÀÌÇÁ(Blow Pipe)³¡¿¡
³ìÀº À¯¸®¸¦ ¹¯Çô °¨Àº ÈÄ, ºÒ¾î¼ ±¸(Ϲ)¸¦ ¸¸µé¸ç, Àû´çÇÑ Å©±â·Î µÇ¾úÀ» ¶§ ¹Ý´ëÆí¿¡ ÆÝƼ(Punty: ¿ëÀ¶(éÂë×)À¯¸®¸¦ ´Ù·ç±â À§ÇØ
»ç¿ëÇÏ´Â ¼è¸·´ë)¸¦ ¿ëÂø(éÂó·)½ÃŰ°í ºí·Î¿ì ÆÄÀÌÇÁ¸¦ ¶¼¾î ³À´Ï´Ù.
´ÙÀ½ ´Ü°è¿¡¼ À¯¸®±¸(Ϲ)¸¦ °¡¿, ºÎµå·´°Ô ¸¸µç ÈÄ ÆÝƼ¸¦ °í¼Ó
ȸÀü½ÃÄÑ ¿ø½É·ÂÀ» ÀÌ¿ë, Æò¸éÀ¯¸®¸¦ »ý»êÇÏ´Â ¹æ¹ýÀÔ´Ï´Ù. óÀ½ºÎÅÍ Å« ¿øÆÇÀ» ¸¸µé ¼ö ÀÖ¾ú´ø °ÍÀº¾Æ´Ï°í Á÷°æ 10~12cm Á¤µµÀÇ ¿øÆÇÀ» ¸¸µç
ÈÄ ±×°ÍÀ» ³³(æç)À¸·Î ¿¬°á, »ç¿ëÇÏ¿´½À´Ï´Ù. ÀÌ´Â ±× ´ç½ÃÀÇ È¸È³ª µ¿ÆÇÈ µî¿¡¼ ÈçÈ÷ º¼ ¼ö ÀÖ´Â ¹Ù, ¿øÆÇÀÇ ÇѰ¡¿îµ¥¿¡ ¹è²Å°úµµ °°Àº ÆÝƼ
ÀÚ±¹ÀÌ ³²¾ÆÀÖ½À´Ï´Ù.
ÀÌ Å©¶ó¿î¹ýÀº Á¡Â÷ ¿¬±¸, °³·®µÇ¾î Á÷°æ 1mÀÇ ¿øÆÇÀ» ¸¸µé ¼ö ÀÖ°Ô±îÁö µÇ¾úÀ¸¸ç ¹è²ÅºÎºÐÀ» ÇÇÇØ »ç°¢ÇüÀ¸·Î
Àý´ÜÇÏ´Â ±â¼úµµ °³¹ßµÇ¾ú½À´Ï´Ù. ±×·¯³ª ±ÕÀÏÇÑ µÎ²²³ª ¸éÀÌ °í¸¥ À¯¸®¸¦ ¸¸µé ¼ö´Â ¾ø¾ú°í ¶Ç Å©±â¿¡ Çѵµ°¡ ÀÖÀ¸¸ç »ý»êÀÌ ºñ´É·üÀûÀ̶ó´Â Á¡ µî,
¸î¸î °áÁ¡ÀÌ ³»ÀçµÈ »óÅ¿´½À´Ï´Ù. ¶Ç ´ç½Ã±îÁöµµ ´ÙÀ̾Ƹóµå¿¡ ÀÇÇÑ Àý´Ü¹ýÀÌ ¹ß°ßµÇÁö ¾Ê¾Æ À¯¸® À§¿¡ ¶ß°Å¿î Àεθ¦ ´í ÈÄ ³Ã¼ö¸¦ ºÎ¾î¼ ¼ÕÁý°Ô·Î
´Ùµë´Â µî Àý´ÜÀ̳ª °¡°øÀÌ ¿ëÀÌÇÏÁö ¾Ê¾Ò½À´Ï´Ù.
|

|
|
1800³â °æ Å©¶ó¿îÛö¿¡ ºñÇÏ¿© ´ëÇü âÀ¯¸®¸¦ ¸¸µé ¼ö ÀÖ´Â ¹æ¹ýÀ¸·Î¼ ½Ç¸°´õ¹ýÀÌ µ¶ÀÏ¿¡¼ °³¹ßµÇ¾ú½À´Ï´Ù. À¯¸®¹°À» ºí·Î¿ì ÆÄÀÌÇÁ ³¡¿¡ ¸»¾Æ¿Ã·Á
Å©¶ó¿îÛö°ú °°ÀÌ ¸ÕÀú À¯¸®±¸(Ϲ)¸¦ ¸¸µç´ÙÀ½, ÀÛ¾÷´ë ¹Ø¿¡ ÀÖ´Â ±íÀº ¿øÅë¼Ó¿¡ ³Ö°í Èçµé¸é¼ °è¼ÓºÒ¾î ¿øÅëÀ» ¸¸µçÈÄ, ¾çÂʳ¡ ºÎºÐÀ» Àß¶ó³À´Ï´Ù.
Àß·ÁÁø ¿øÅëÀº Á÷°æÀÌ 30~50cm, ±æÀ̰¡ 120~180cm Á¤µµÀε¥ À̸¦ ±æÀÌ ¹æÇâÀ¸·Î Àý´ÜÇÏ¿© ¿ä(é¢ : µµÀڱ⸦ ±Á´Â °¡¸¶)¼Ó¿¡¼
Àç°¡¿ÇÏ¸é ÆòÆòÇÑ ÆÇÀÌ µË´Ï´Ù.
ÀÌ ¹æ¹ýÀº Å©¶ó¿îÛö º¸´Ù Å« À¯¸®¸¦ ¸¸µé ¼ö ÀÖ¾ú°í Áß¾ÓÀÇ ÆÝƼ ÀÚ±¹µµ ¾øÀ» »Ó ¾Æ´Ï¶ó Á¦Á¶¿ø°¡µµ
³·¾Ò½À´Ï´Ù. ±×·¯³ª ³Ã°¢°ú Àç°¡¿ÀÇ ¹Ýº¹ÀÛ¾÷À¸·Î ÀÎÇÏ¿© À¯¸®ÀÇ Ç¥¸éÀÌ °í¸£Áö ¸øÇÏ°í µÎ²²ÀÇ Â÷µµ ½ÉÇÏ¿´½À´Ï´Ù.
|

|
|
20¼¼±â¿¡ À̸£·¯ ÆÇÀ¯¸®ÀÇ Á¦Á¶¹ýÀº ±Þ¼ÓÈ÷ ¹ßÀü, ´ë·®»ý»ê ½Ã´ë·Î µ¹ÀÔÇß½À´Ï´Ù. ÇÚµå ½Ç¸°´õ¹ýÀº ¸¹Àº ¼÷·Ã°øÀ» ÇÊ¿ä·Î Çϰí Á¦Á¶½Ã°£ ¶ÇÇÑ
±æ¾ú½À´Ï´Ù. ÀÌ ¹«·Æ Àΰ£ÀÌ ¼ûÀ» ºÒ¾î³Ö´Â ´ë½Å ¾ÐÃà°ø±â¸¦ »ç¿ëÇÏ´Â ¹æ¹ýÀÌ °³¹ßµÇ¾ú½À´Ï´Ù. ÀÌ´Â 19¼¼±â ¸»¿±, À¯·´¿¡¼µµ °í¾ÈµÈ ¹Ù ÀÖÀ¸³ª
°ø¾÷ÈÇÑ °ÍÀº 1903³â ¹Ì±¹ÀÇ ¶ó¹ö(Lubber)¿Í ¡¸¾Æ¸Þ¸®Ä À©µµ¿ì ±Û·¡½ºÞ䡹¿´½À´Ï´Ù. À¯¸®¹°À» ·Î(furnace)¿¡¼ ÀÏ´Ü Å« ±¹ÀÚ¸¦
»ç¿ë, µµ°¡´Ï·Î ¿Å±ä ÈÄ, ½Ç¸°´õ¸¦ ¹Ð¾î ³Ö°í ¾ÐÃà°ø±â¸¦ ºÒ¾î³ÖÀ¸¸é¼ ¼¼È÷ ´ç°Ü ¿Ã¸®´Â ¹æ¹ýÀÔ´Ï´Ù.
ÀÌ´Â ÃÖÃÊÀÇ ±â°èȵÈ
¼ºÇü¹ý(à÷úþÛö)À¸·Î¼ Á¦1Â÷¼¼°è´ëÀü ÈıîÁö »ç¿ëµÇ¾ú½À´Ï´Ù. ÀÌ ¹æ¹ýÀ¸·Î¼ ±æÀÌ 12m,Á÷°æ 0.9mÀÇ ±ä À¯¸®±îÁö ¸¸µé ¼ö ÀÖ¾ú½À´Ï´Ù. ¸Ó½Å
½Ç¸°´õ¹ý(Machine Cylinder Method)¿¡ ÀÇÇÑ ÆÇÀ¯¸®ÀÇ »ý»êÀº ǰÁúÀÌ ¿ì¼öÇÑ ¿¬¼Ó½Ä Àλó¹ý¿¡ ÀÇÇÑ ÆÇÀ¯¸® »ý»êÀÌ ½ÃÀ۵DZâ±îÁö
±Þ°ÝÈ÷ Áõ°¡µÇ¾úÀ¸³ª 1929³â¿¡ À̸£·¯ »ý»êÀÌ ÁßÁöµÇ¾ú½À´Ï´Ù. 1925³âÀÇ ÆÇÀ¯¸® »ý»ê·® Áß 59%´Â ¸Ó½Å ½Ç¸°´õ¹ý, 29%´Â Äݹø¹ý, 10%´Â
Ç®Äݹý, 2%´Â ÇÚµå ½Ç¸°´õ¹ý¿¡ ÀÇÇÑ °ÍÀ̾ú½À´Ï´Ù.
|

|
|
¿¬¼Ó½Ä ¼öÁ÷Àλó¹ýÀÎ Ç®ÄݹýÀº 1903³âºÎÅÍ ¿¬±¸°¡ ½ÃÀ۵Ǿî 1904³â ƯÇ㸦 ÃëµæÇϱ⿡ À̸£¸¨´Ï´Ù. ±×·¯³ª ¿Ï¼ºµÇ±â±îÁö º¯Çϱ⠽¬¿î À¯¸®ÀÇ
ÀÛ¾÷¿Âµµ, Àλó±â ¹ØºÎºÐ ÁÖÀ§ÀÇ ³Ã°¢, À¯¸®ÀÇ Á¶¼º¹®Á¦ µî ¸¹Àº ³Á¦¿¡ ºÎµúÄ¡°Ô µË´Ï´Ù. ±×·³¿¡µµ ³ë·ÂÀ» °Åµì, Á¦1Â÷¼¼°è´ëÀüÁ÷Àü(1913³â)
º§±â¿¡¿¡¼ ÃÖÃÊ·Î ½Ç¿ëÈÇÒ ¼ö ÀÖ°ÔµÇ°í µ¶ÀÏÀΰúÀÇ Çù·Â¿¡ ÀÇÇÏ¿© ±× ½Ç¿ë¼ºÀº ´õ¿í Çâ»óµÇ¾ú½À´Ï´Ù. ±×·¯³ª ÀüÀïÁß µ¶ÀÏ Á¡·ÉÇÏ¿¡ ÀÖ´Ù°¡ ÀüÀïÀÌ
³¡³ ÈÄ ´Ù½Ã º§±â¿¡·Î µ¹¾Æ¿Â Ç®ÄÝÀº Àû±¹¿¡ Çù·ÂÇß´Ù´Â Á˸ñÀ¸·Î Åõ¿ÁµÇ¾î °á±¹ °¨¿Á¿¡¼ º´»çÇÕ´Ï´Ù. ÀÌ ¹æ¹ýÀº °á±¹ Ç®ÄÝÀÌ º´»çÇÑ Á÷ÈÄÀÎ
1919³â ¿Ï¼ºµË´Ï´Ù.
µ¥ºñÆ©½º(Debiteuse)¶ó°í ºÎ¸£´Â ³»È¹°(Ò±ûýÚª)À» ·ÎÀÇ ³¡ºÎºÐ¿¡ ÀÖ´Â µå·ÎÀ× Å³¸¥(Drawing
Kiln)¿¡ ³Ö°í µ¥ºñÆ©½ºÀÇ ½½·ÎÆ®(Slot)·ÎºÎÅÍ º£ÀÌÆ®(Bait)¸¦ »ç¿ëÇÏ¿© ¿øÆÇÀ» ÀλóÇÕ´Ï´Ù. À̶§ µ¥ºñÆ©½º »óºÎ¿¡ ÀÖ´Â ½ÃÆ®
Äð·¯(Sheet Cooler)´Â À¯¸®¸¦ ³Ã°¢ÇÏ¿© Àû´çÈ÷ °æÈ(Ìãûù)½ÃŰ¸ç ¿§Áö(Edge)¸¦ Àâ¾ÆÁÖ´Â µÎ½ÖÀÇ ³Î·¯¡¼Knurler ¶Ç´Â
½ºÆ®·¹Ã³(Stretcher)¡½´Â ¿øÆÇÀÇ ÆøÀ» ÀÏÁ¤ÇÏ°Ô À¯ÁöÇÏ¸ç ¾à 6m³ôÀÌÀÇ ¼³Ãž ¼ÓÀÇ ¾Æ½ºº£½ºÅ佺 ·Î¿ï·¯(Asbestos Roller)»çÀ̸¦
Åë°úÇÏ¿© ¿øÆÇ½Ç·Î ¿Ã¶ó°©´Ï´Ù. ¿øÆÇÀÇ µÎ²²´Â ÁÖ·Î Àλó¼Óµµ¿¡ ÀÇÇÏ¿© °áÁ¤µÇ¸ç 2mmÀÇ Àλó¼Óµµ´Â ºÐ´ç 65¢© Á¤µµÀ̰í, ¸Ó½Å(Machine)ÀÇ
ÆøÀº Åë»ó 80~90¢©ÀÔ´Ï´Ù.
ÀÌ ¹æ½ÄÀÇ Æ¯Â¡Àº ±× ¿ëÇØ´É·Â¿¡ µû¶ó¼ ÇϳªÀÇ ¿ëÇØ·Î¿¡ ´Ù¼öÀÇ Àλó±â¸¦ ºÎÂø½Ãų¼ö ÀÖ´Ù´Â Á¡ÀÌ´Ï,
9~12°³ÀÇ Àλó±â¸¦ ºÎÂø½Ãų ¼ö ÀÖ¾ú½À´Ï´Ù. µ¥ºñÆ©½ºÀÇ ½½·ÎÆ®´Â ÁÖº¯ÀÇ Ä§½Ä, ȤÀº ½ÇÅõ»ý¼º(ã÷÷âßæà÷)µî¿¡ ÀÇÇÏ¿© º¯ÇüÇϱ⠽±½À´Ï´Ù. µû¶ó¼
¿øÆÇÀÇ µÎ²²¿¡ ºÎºÐÀûÀÎ ºÒ±ÕµîÀÌ ¹ß»ýÇϸç, ÀÛÀº »ý¼º¹°ÀÌ ¿øÆÇ¿¡ ºÎÂøÇÏ´Â µî °áÁ¡ÀÌ Àֱ⠶§¹®¿¡ ¾î´À Á¤µµ »ç¿ëÇÑ µ¥ºñÆ©½º´Â Àû´çÇÑ ½Ã±â¿¡
±³Ã¼ÇØ¾ß ÇÕ´Ï´Ù. Ç®Äݹý, Äݹø¹ý ¹× ½Ç¸°´õ¹ýÀº 1930³â´ë¿¡ ¼·Î °æÇÕÀ» ¹ú¿´À¸³ª Ç®ÄݹýÀÌ ´Ü¿¬ ¿ì¼¼, Á¦2Â÷¼¼°è´ëÀü Á÷Àü±îÁö 42°³±¹¿¡
800¿©±âÀÇ ¸Ó½ÅÀÌ ¼³Ä¡µÇ¾ú½À´Ï´Ù.
|

|
|
Äݹø¹ýÀº 1905³â ¹Ì±¹ÀÇ ÄݹøÀÌ Æ¯Ç㸦 ¾òÀº ÈÄ 1916³â ¸®ºñ ¿ÀÀ¢½º(Libbey-Owens)¿¡ ÀÇÇØ¼ °³·®µÇ¾î ¿ÏÀüÈ÷ ¼º°øÀ» °ÅµÎ¾ú½À´Ï´Ù.
Ç®Äݹý°ú ´Ù¸¥ Á¡Àº µ¥ºñÆ©½º¸¦ »ç¿ëÇÏÁö ¾Ê°í ¿øÆÇÀ» ¿ëÀ¶À¯¸®¸é¿¡¼ Á÷Á¢ ÀλóÇÕ´Ï´Ù. ÀλóµÈ ¿øÆÇÀº ¿ëÀ¶À¯¸®¸é¿¡¼ 70cm°Å¸®¿¡ ÀÖ´Â º¥µù
·Î¿ï(Bending Roll)¿¡ ÀÇÇØ¼ Á÷°¢À¸·Î ±ÁÇôÁø ÈÄ ¼öÆò ·Î¿ï¿¡ ÀÇÇØ ¾à 60mÀÇ ¾Æ´Ò¸µ ·¹¾î(Annealing Lehr)¸¦ Åë°úÇÕ´Ï´Ù.
ÀÌ ¶§ ¿øÆÇÀÇ ¾ç ³¡Àº ³Î·¯¿¡ ³¢¿öÁ®¼ ÀÏÁ¤ÇÑ ÆøÀ» À¯ÁöÇÏ°Ô µË´Ï´Ù.
¿øÆÇÀÇ µÎ²²´Â ÁÖ·Î Àλó¼Óµµ¿¡ ÀÇÇØ¼ °áÁ¤µÇÁö¸¸ ¿øÆÇÀÇ µÎ²²¸¦ ÀÏÁ¤ÇϰÔ
Çϱâ À§Çؼ´Â ¿øÆÇÀÇ Æø ¹æÇâÀ¸·Î ¿ëÀ¶À¯¸®¸¦ µ¿ÀÏÇÏ°Ô ³Ã°¢½ÃÄÑ¾ß ÇÏ´Â ¹Ù À̰ÍÀÌ Äݹø¹ýÀÇ ÁÖ¿ä Æ÷ÀÎÆ®ÀÔ´Ï´Ù. 2mmÀÇ Àλó¼Óµµ´Â ºÐ´ç 130¢©
Á¤µµÀÌ¸ç ¿øÆÇÆøÀº Åë»ó 100~158¢© ÀÔ´Ï´Ù. ¶ÇÇÑ ÀÌ ¹æ¹ý¿¡ µû¸£¸é À¯¸®°¡ ¼öÆòÀ¸·Î »ý»êµÇ±â ¶§¹®¿¡ ¾Æ´Ò¸µ ·¹¾î¸¦ ±æ°Ô ÇÒ¼öÀÖ¾î ¼³ÃÀÌ
°¡´É, Àý´ÜÀÌ ¿ëÀÌÇÕ´Ï´Ù. ±×·¯³ª ·»µù ·Î¿ï¿¡ À̹°ÀÌ ºÎÂøÇѴٵ簡, ·Î¿ï Ç¥¸éÀÌ ±ÜÈ÷¸é ±×°ÍÀÌ ±×´ë·Î ¿øÆÇ¸é¿¡ ³ªÅ¸³ª±â ¶§¹®¿¡ º¥µù ·Î¿ïÀ»
¼ö½Ã·Î ¿¬¸¶, ±³Ã¼ÇÏ¿©¾ß ÇÕ´Ï´Ù. Äݹø¹ýÀº ÇϳªÀÇ ·Î¿¡ 1~4°³ÀÇ Àλó±â¸¦ ºÎÂøÇÒ ¼ö ÀÖ½À´Ï´Ù.
|

|
|
¡¸PPGÞ䡹´Â Ç®Äݹý°ú Äݹø¹ýÀÌ °³¹ßµÉ ´ç½Ã ÀÌ¹Ì ¸¶ÆÇÀ¯¸® ¸ÞÀÌÄ¿·Î¼ÀÇ À§Ä¡¸¦ È®¸³, ´ë±Ô¸ð ¼³ºñ¸¦ °®°í ÀÖ¾ú½À´Ï´Ù. ±×·¯³ª Ç®Äݹý°ú Äݹø¹ýÀÇ
ƯÇã±ÇÀ» ÀμöÇϱ⠾î·Á¿î »óȲÀ̾ú±â ¶§¹®¿¡ 1918³â~1925³â¿¡ °ÉÃÄ ±×·¹°í¸®¿ì½º(Gregorious)·Î ÇÏ¿©±Ý »õ·Î¿î ÆÇÀ¯¸® Àλó¹ýÀÇ °³¹ßÀ»
ÁøÇà½ÃŲ ¹Ù, ¸¶Ä§³» 1926³â ƯÇ㸦 ÃëµæÇÕ´Ï´Ù. ÀÌ´Â Ç®Äݹý°ú °°Àº ¼öÁ÷Àλó¹ýÀÌÁö¸¸ Ç®ÄݹýÀÇ µ¥ºñÆ©½º¸¦ »ç¿ëÇÏÁö ¾Ê°í µå·Î¿ì ¹Ù(Draw
Bar)¶ó°í ºÎ¸£´Â ³»Èº®µ¹À» µå·ÎÀ× Å³¸¥ÀÇ À¯¸®¹°¼Ó¿¡ Àá±â°Ô ÇÏ´Â °ÍÀÔ´Ï´Ù. µû¶ó¼ ÀÚÀ¯Ç¥¸éÀ¸·ÎºÎÅÍ À¯¸®°¡ ÀλóµÇ´Â¹Ù ÀÌ Á¡Àº Äݹø¹ý°ú
À¯»çÇÕ´Ï´Ù.
ÀÌ ÇÇÃ÷¹ö±×¹ýÀº 1930³â °æ ½Ç¿ëȵǾúÀ¸³ª Ç®ÄݹýÀ̳ª Äݹø¹ý¿¡ ÀÇÇÑ ÆÇÀ¯¸®¿¡ ºñÇÏ¿© ǰÁúÀ̳ª »ý»êÈ¿À²ÀÌ ¶³¾îÁ³½À´Ï´Ù.
±×·¯³ª ±×ÈÄ ¡¸ÇÊÅ·Åæ(Philkington)Þ䡹°¡ À̸¦ µµÀÔ, °³·®ÇÔÀ¸·Î½á ¿À´Ã³¯¿¡ À̸£·¯¼´Â È¿À²À̳ª ǰÁúÀ» ¸Å¿ì ³ôÀº ¼öÁØ¿¡±îÁö ²ø¾î¿Ã¸®°Ô
µÇ¾ú½À´Ï´Ù. °³¹ß Ãʱ⿡´Â ·Î´ç 4±âÀÇ ¸Ó½ÅÀ» ºÎÂøÇßÀ¸³ª ³ªÁß¿¡´Â 8±â·Î ´Ã¾î³µÀ¸¸ç, ±× ÈÄ¿¡´Â 10±âÀÇ ¸Ó½Å±îÁöµµ ºÎÂø½Ãų¼ö ÀÖ¾ú½À´Ï´Ù.
|
|
|